Vacuum furnace systems allow for high temperature processing in fully controlled oxygen-free environments. The hot zone of the furnace is contained entirely within a sealed water-cooled vessel which allows for a controlled atmosphere with minimal insulation to reduce cool down time of the system. Vacuum furnaces provide high consistency and low contamination for annealing, brazing, sintering, and heat treatment processes.
Thermal Technology specializes in premium equipment for customers that demand the highest level of temperature and environmental control within their furnaces. With an average furnace lifetime of 20+ years our customers are long-term partners that we continue to support for the lifetime of the equipment.
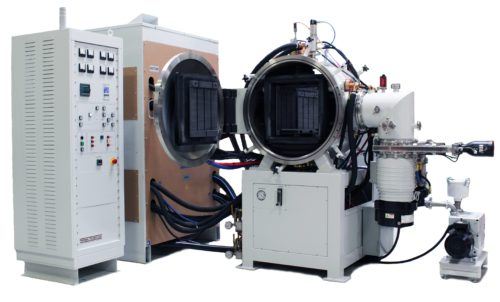
Vacuum Furnace Applications
Our furnaces are used in everything from research and development of new materials at major universities and national labs to the manufacturing of parts for industry. Currently, our furnaces are being used in a wide range of applications, including but not limited to:
- Ceramic Ballistic Armor
- Carbon-Carbon, SiC fiber and Composites
- Ceramic Sintering
- Powder Metallurgy
- Synthesis Reactions
- Vacuum Brazing
- Heat Treatment
- Melting
- Chemical Vapor Deposition
- Ultra High temperature Processing
- Orthodontia
- Vacuum Power Interrupters
- X-Ray Tubes
- Gas & Liquid Chromatography
& - Micro Channel Heat Exchangers
- MIM: Metal Injection Molding
- Ceramics & Metals Brazing
- Cermets
- Medical Implants
Hot Zone Materials
The material of the hot zone typically determines the application and operating conditions of the furnace, the two main materials are either graphite or refractory metal systems. Graphite hot zone vacuum furnaces are the most common in industry as they are durable and low cost, however for materials and applications that demand a truly clean environment refractory metal hot zone vacuum furnaces are the preferred alternative.
The material of the hot zone typically determines the application and operating conditions of the furnace, the two main materials are either graphite or refractory metal systems.
Graphite Vacuum Furnaces
Graphite hot zone vacuum furnaces are the most common in the industry as they are durable and low cost, however for materials and applications that demand a truly clean environment, refractory metal hot zone vacuum furnaces are the preferred alternative.
Molybdenum and Tungsten Vacuum Furnaces
High temperature vacuum furnaces require the use of refractory metals for the hot zone materials. These hot zones enable production at higher temperatures with sustained durability, and flexibility of application. Two of the most common refractory metals used today are Molybdenum and Tungsten.
Hot Zone Material | Maximum Temperature | Typical Applications |
Graphite | 3,000°C | High temperature sintering, heat treatment |
Molybdenum | 1,800°C | Powder metallurgy, diffusion bonding |
Tantalum | 2,500°C | Processing Electronic materials |
Tungsten | 3,000°C | Sintering and heat treating carbon sensitive materials |
Thermal Technology offers a range of vacuum furnaces to fit almost any application from our standard product line to Custom-Designed Vacuum Furnaces. Where a custom furnace is needed, Thermal Technology can produce a custom vacuum furnace to fit your specific application. Contact us to discuss your application and the requirements.
Download Product Brochure
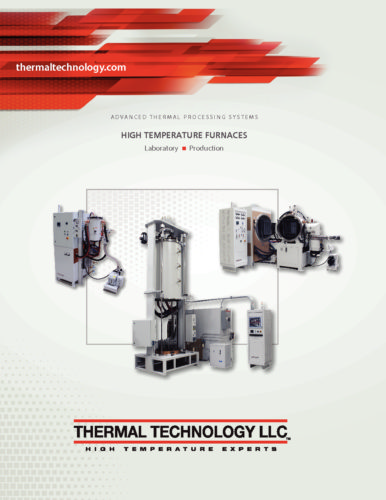